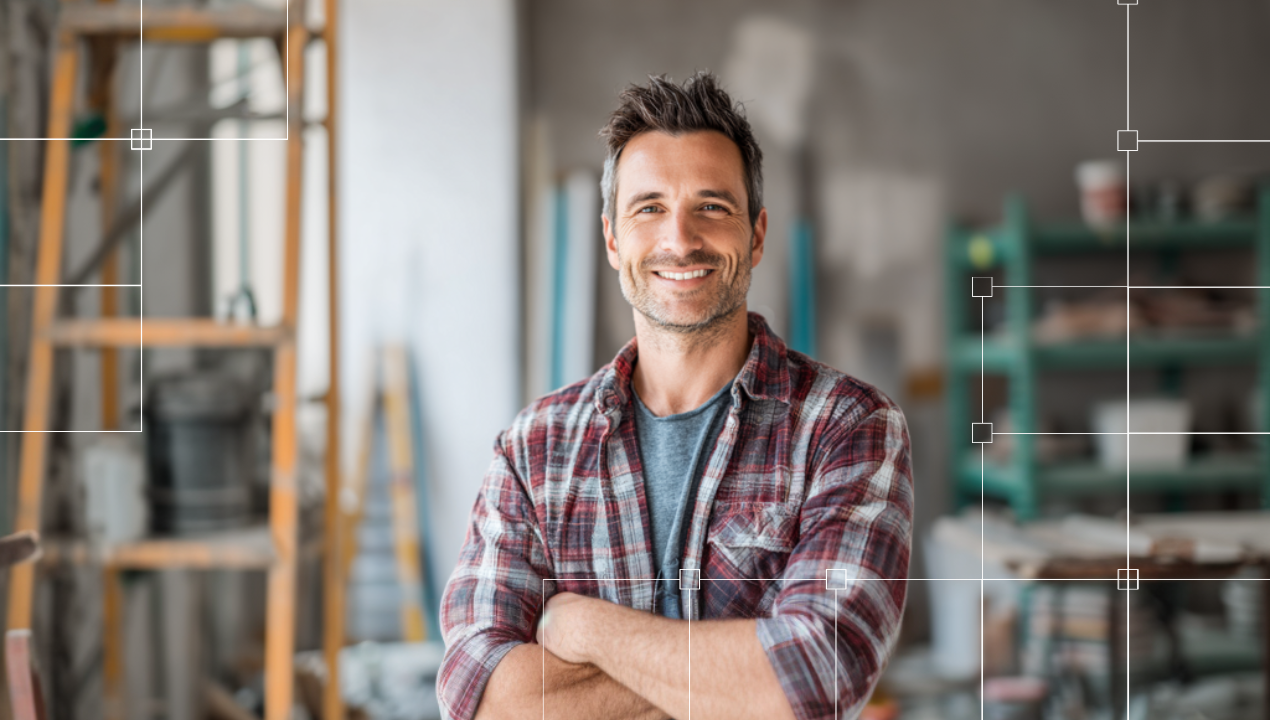
Why construction costs remain high in the US today
Demand for housing skyrocketed, and as we get close to the new year, the trend remains upward. This is due to the increase in the number of millennials who took advantage of the low mortgage interest rates. Indeed, many are still looking to secure a home in today’s market despite the low home inventory and high interest rates, which leads to the question—will construction costs also go down?
The Supply Chain
For some sectors today, the congestion seems to be improving.
However, there are still nearly two million containers headed to the United States. Once they arrive, inventories that haven't been affected by raw material shortages will be replenished.
This will cause the costs in the supply chain to rise again. Additionally, the period of low prices has caused others to start buying more. This is the case for both businesses and consumers, which is a sure sign that the cost of goods will increase to accommodate the higher demand.
The Cost of Materials
The supply chain backlog creates a link to the rising cost of materials. So far, the projected cost of construction in 2022 is still high.
The prices of lumber and steel, for example, have increased more than at any other time since the government began recording data in 1949. The cost of plastic is greater than it has been at any time since 1976.
Furthermore, oil prices have reached unprecedented levels, resulting in a significant increase in the cost of transportation to deliver materials to the marketplace.
Also, Natural disasters like hurricanes, tornadoes, and wildfires have become more frequent, which raises the demand for building materials. But sometimes, these same disasters destroy the resources needed to rebuild, creating what is known as a perfect storm.
The Cost of Labor
The rising cost of labor is also attributed to the low unemployment rate, which is at its lowest point since 1969. This is due to a mismatch between the skills of the job seekers and the skills required for the available jobs.
If the unemployment rate falls too low, it can lead to a cohort of potential employees that cause wages to rise. However, this is not always a bad thing.
A higher wage also means a higher standard of living. With this being said, the rising cost of labor is one of the main challenges that the industry must address, especially when demand is so high.
The Cost of Lumber, Steel, and Copper
Construction costs will continue to rise in the United States due to the rising cost of lumber, steel, and copper. To make matters worse, higher costs are also a result of shortages currently hitting the industry.
There is a need to develop better materials with a longer lifespan, which will cut the cost of maintaining materials and increase the lifespan to save maintenance costs.
As the world’s demand for steel increases, the cost of steel is expected to rise even further. There is a need to improve steel fabrication and develop more innovative ways to meet the growing demand.
With the decline in demand for copper, inventories are low and any increase in demand will likely drive the price of copper even higher. In anticipation of this, many companies are investing in technologies to improve efficiency and reduce costs.
The Bottomline
To conclude, the cost of building materials will increase in the US market over the next five years.
The reasons are many, but the lack of a sufficient workforce, the cost of materials, and the increasing demand are the main factors that are contributing to increasing the cost of building materials.
If you need residential remodeling, we can help you here at Bolster. Bolster is the only estimating software available today that allows you to send visual, interactive estimates that provide an Amazon-like buying experience. It can also save you hours on construction estimating. Find out how much time you are wasting estimating and how you can fix that now here! It only takes 1 minute and 30 seconds.