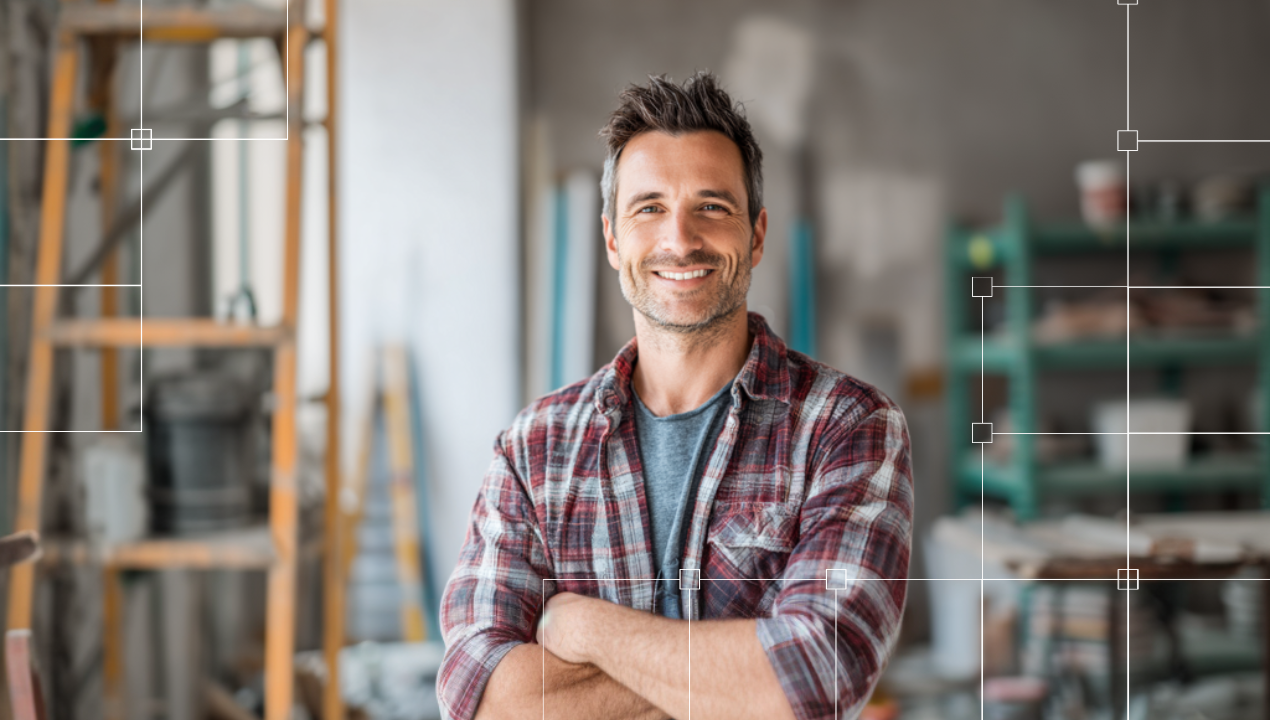
Improving Efficiency in Construction: Tips to Boost Productivity
Eliminate Delays and Maximize Efficiency
In construction, time is money. Every delay, miscommunication, or rework can eat into your profit margins and schedule commitments. Residential contractors know the frustration of juggling multiple projects while battling common inefficiencies, such as crews waiting around for materials and endless phone tag with subcontractors. The positive news is that there are concrete steps you can take to boost productivity in construction and eliminate those time-wasters. In this post, we’ll discuss the biggest inefficiencies contractors face and provide actionable strategies to improve workflow, communication, and scheduling. By leveraging these tips (and using modern tools like Bolster), you can transform your operations, get projects done faster, and increase your bottom line.
The High Cost of Inefficiency
Construction projects are notorious for running late and over budget, often due to avoidable inefficiencies. In fact, “construction projects are notorious for their delays and cost overruns—both symptoms of larger inefficiencies at work.” Inefficiency, whether on the jobsite or in the office, not only leads to headaches but also directly impacts your business.
- Lost Time: When schedules slip, you’re paying more in labor and overhead for the same job. Idle time (workers waiting on instructions or materials) is essentially money burning. If a crew is standing around for an hour each day due to poor coordination, that’s a significant loss over a month-long project.
- Higher Costs: Inefficiencies often result in rework, which involves repeating tasks due to errors or miscommunication. In some cases, rework can account for 5–10% of project costs. Furthermore, last-minute rush orders on materials (due to poor planning) can incur extra fees. All these costs chip away at your profit.
- Strained Client Relationships: Delays and disorganization erode client confidence. Homeowners expect their contractor to maintain a high level of organization. If you miss deadlines or appear disorganized, client satisfaction plummets. Such behavior can result in fewer referrals and even negative reviews, affecting future business.
- Worker Frustration: Your team also feels the pain. Talented tradespeople don’t enjoy working on a chaotic site or redoing work. Inefficiencies can lower morale and productivity further, creating a vicious cycle. In the worst cases, you risk higher turnover if crews are constantly frustrated by poor management.
Identifying the biggest time-wasters in your construction business is the first step. Common culprits include:
- Last-minute changes or lack of planning: starting a project without a detailed plan often leads to scrambling later.
- Poor communication: for example, the crew at site A doesn’t know that a delivery is delayed, so they can’t move forward and stand idle.
- Scheduling conflicts: subs arriving out of sequence or crews interfering with each other due to a bad schedule.
- Manual administrative work: spending hours on paperwork, data entry, or searching through emails for information.
- Inefficient resource management, like not having the needed equipment on site or equipment breakdowns halting work because maintenance was skipped.
- Underutilizing labor can waste the talents on your team by not delegating tasks effectively or not matching skill sets to the job at hand.
- Waiting on approvals: delays in getting client or inspector approvals can stall progress if not managed proactively.
The construction industry has historically lagged in productivity growth compared to other sectors, but that means there’s giant room for improvement. Improving efficiency is about working smarter, not necessarily harder, by removing obstacles so that every hour of work generates the results it should.
Strategies to Improve Construction Efficiency
Tackling inefficiency requires a multifaceted approach. Here are several key strategies and solutions to greatly improve your workflow and productivity on construction projects:
1. Plan Projects Thoroughly from the Start
“Measure twice, cut once” applies not just to carpentry but to project planning as well. Rushing through the planning phase is a major efficiency killer. Errors made in the project setup cascade into bigger issues later. Instead, invest time upfront to develop a comprehensive plan:
- Detailed Scope and Budget: Clearly define the project scope, client selections, and budget. Early decision-making reduces mid-project changes. Use pre-construction meetings to nail down client expectations and specifications.
- Critical Path Schedule: Create a realistic schedule that accounts for lead times (for permits, materials like windows or trusses, etc.) and includes some buffer for weather or unforeseen issues. Sequence trades logically to minimize downtime. For instance, avoid scheduling painters when you are aware that the drywall compound requires an additional week to dry. A well-thought-out schedule keeps everyone productive.
- Resource Allocation: Plan your labor and equipment needs in advance. Ensure you’ll have the right crew size and skills on site each phase. Please arrange for subcontractors in advance and verify their availability. If you foresee any gaps, you have time to adjust (hire extra help, rent equipment, etc.) rather than improvising later.
- Procurement Planning: List all long-lead materials or custom orders and order them early. Nothing slows a job like waiting 8 weeks for windows that were ordered too late. Use the project plan to create a procurement schedule.
- Risk Assessment: Identify potential bottlenecks or high-risk aspects of the job (like a tricky structural element or a dependency on a utility company’s work) and have contingency plans. By anticipating problems, you can avoid being unprepared.
Yes, planning takes effort, but it pays off massively. As one tip puts it, “Devote plenty of time to planning to figure out the people, processes, information, and materials you’ll need before the project begins.” Slowing down at the start can actually speed everything else up.
2. Improve Communication Channels
Miscommunication silently undermines efficiency. A message not delivered to the right person at the right time can halt progress. To boost efficiency:
- Adopt Real-Time Communication Tools: Relying on phone tags or scattered text messages leads to confusion. Consider using a centralized communication tool or app (like Bolster’s messaging) where project stakeholders, including subs and clients, can share updates. Mobile technology with messaging and commenting capabilities reduces miscommunication between team members, subs, and clients. For instance, you can instantly broadcast a design change to all relevant parties, preventing the crew from building the old design.
- Regular Team Meetings: Hold quick daily huddles or weekly coordination meetings. These check-ins ensure everyone knows the current priorities and any changes. It’s also a chance for field staff to voice concerns (maybe they noticed a potential issue that management isn’t aware of). Your staff in the field are your eyes and ears; listen to them to improve workflow. Create an environment where they feel heard.
- Client Updates: Efficient projects keep clients in the loop, which, ironically, can save you time. When clients know what’s happening, they’re less likely to flood you with ad hoc questions. Use a client portal or schedule regular update calls to inform them of progress, upcoming decisions needed, or any hiccups. Clear communication with clients also accelerates approval processes; if you need a quick decision on a change, a client who’s regularly informed can answer faster.
- Documentation Sharing: Use cloud storage for plans, permits, and documents so everyone accesses the latest versions. Field crews shouldn’t be working off an outdated drawing because someone forgot to send the updated PDF. A centralized file system (even something like Google Drive or a construction management app) ensures the latest info is at hand. This prevents rework due to miscommunication on specs or plans.
- Defined Communication Protocols: Set rules for how communication happens. For example, establish that all change orders must be documented and sent via email or through the project management system (not verbally on site). Or decide that the site supervisor is the point of contact for all subcontractors (to avoid confusion when multiple people are giving directions). A clear chain of command and communication protocol keeps information flowing in an organized way.
By keeping a constant flow of communication, you synchronize your team and avoid many stoppages caused by uncertainty. Modern construction management is as much about managing information as managing bricks and beams. When everyone is on the same page, work gets done faster and with fewer mistakes.
3. Embrace Technology and Automation
In an industry known for clipboards and spreadsheets, one of the biggest efficiency boosts comes from adopting the right technology. Construction efficiency tools can save hours each day by streamlining tasks and reducing manual labor.
- Project Management Software: Tools like Bolster provide an all-in-one platform for estimating, scheduling, budgeting, document management, and communication. Instead of juggling Excel, email, and random texts, everything lives in one system accessible to your team. Construction software keeps track of daily tasks, schedules, budgets, and communications in one centralized place, automating workflows along the way. This results in reduced time spent on data entry across various platforms and a reduced likelihood of errors occurring.
- Scheduling Apps: Ditch the whiteboard or static calendar. A dynamic scheduling app will send alerts for upcoming tasks, allow easy adjustments, and even let subs update their status. Everyone sees the latest schedule in real time. This reduces downtime because if one task finishes early or late, you can immediately shuffle the plan and notify the affected parties.
- Mobile Field Apps: Equip your field staff with mobile apps for daily logs, time tracking, and progress reports. Instead of driving to the office to drop off timesheets or reports, they submit them instantly on their phones. Not only does your company save admin time, but you also get faster insight into field data. For example, if a crew notes in the daily log that they’re held up waiting for an inspector, you can react the same day to resolve it.
- Automation and Templates: Use templates for routine processes, estimation sheets, checklists, RFIs, etc. Many software tools let you create templated workflows. Automation can send emails to clients at certain milestones or auto-generate purchase orders when a phase is approved. Every task that you automate or standardize is one less thing someone has to remember to do manually. It also ensures consistency (fewer errors).
- Cost Tracking and Accounting Software: Efficient financial management is part of project efficiency. Use accounting software or integrated cost tracking to monitor budget vs. actual in real time. This feature helps catch cost overruns early and avoids the time-consuming scramble of sorting finances after project end. If your software flags that a budget line is nearly exhausted, you can address it now rather than do forensic accounting later.
- Design and Visualization Tech: Consider using digital design tools or even BIM (Building Information Modeling) for complex projects. Catching coordination issues in a digital model can prevent massive time loss on site. Likewise, using client-friendly visualization (like 3D renderings) can help clients finalize decisions faster, reducing the back-and-forth during construction.
The bottom line: “Technology-supported processes are proven to increase efficiency.” If you’ve been hesitant to adopt new tech, start with one area that causes you the most headaches (scheduling? reporting? communication?) and try a solution for that. Time savings and mistake avoidance quickly offset the initial learning curve. In today’s market, contractors leveraging technology have a clear advantage in delivering projects on time.
4. Optimize Scheduling and Time Management
Effective time management on a construction site is just as crucial as maintaining a well-functioning machine. To improve efficiency, consider the following strategies:
- Avoid Crew Downtime: Analyze your typical day and see where crews wait unnecessarily. If your framing crew frequently waits for the superintendent's instructions in the morning, consider implementing a quick morning meeting or a daily task list to ensure they can start work immediately. If materials often arrive midday, causing a lull, adjust delivery times or have secondary tasks (like site clean-up) planned for those gaps.
- Overlap Tasks Strategically: Search for opportunities to overlap work without causing interference. For instance, can the electricians start rough-in on the second floor while drywall is finishing on the first floor? Careful scheduling can shave days off the timeline by not strictly doing everything sequentially. Just be cautious to coordinate so crews aren’t in each other’s way.
- Enforce Deadlines with Subs: Subs have other clients too, so make sure you’re obvious about your schedule needs. If a sub knows you have a firm inspection on Friday, they’re more likely to show up with enough labor to meet it. To foster accountability, consider scheduling progress check-ins a day or two before the deadline; this allows a buffer to adjust if needed.
- Use Gantt charts or visual schedules: A visual timeline (easy to create in project management software or even Excel) helps everyone see the plan. It can also highlight critical path items. When the team sees visually that if Task A slips two days, it will push Task B, they understand the urgency. It’s a great communication tool that keeps focus on the schedule.
- Implement Time Tracking: For your crew, use a clock app or system. Not only will these steps ensure accurate payroll, but reviewing timesheets can reveal inefficiencies (e.g., too much overtime on a certain phase indicating a scheduling issue or too many hours on non-productive tasks). Adjust your labor scheduling accordingly to match the workload.
- Limit Overtime and Overscheduling: Paradoxically, pushing crews to constant overtime can reduce efficiency due to fatigue and burnout. It might lead to more mistakes or even safety incidents (which can significantly delay a project). It’s often more efficient to bring an extra hand than to have a smaller crew work 12-hour days continuously. Please manage your team’s time to ensure sustainable productivity.
Remember, the goal is to complete projects on time (or ahead of time) without rushing at the last minute. Good scheduling is like the backbone of project efficiency; when everyone knows what to do and when, there’s less idle time and confusion.
5. Invest in Training and Process Improvement
Efficiency isn’t just about speed; it’s also about doing things right the first time and empowering your team. Focus on these two areas:
- Employee Training: A well-trained crew works faster and makes fewer mistakes. Take the time to train workers on the best practices of their trade, on how to use new tools or software, and on safety procedures. Training might seem like taking time away from “real work,” but it improves quality and speed long-term. Even cross-training your team (so a laborer can assist the carpenter, for example) can improve flexibility on site. Engaged, skilled workers will find ways to work more efficiently and adapt better to challenges.
- Process Standardization: Examine the execution of tasks to identify potential improvements. Could a different construction method save time without sacrificing quality? For instance, using prefabricated components or modular construction for certain elements might speed up on-site work. Standardize repetitive tasks, create checklists for site setup or closeout, use templates for reporting, etc. Maintaining consistency ensures that your team adheres to established, efficient procedures rather than reinventing each project.
- Continuous Improvement: After each project, do a brief postmortem with your team. What caused delays? What went well? By learning from each project, you continually refine your processes. Maybe you’ll discover that a particular inspection always slows you down; next time you’ll schedule it earlier or ensure everything is 100% ready to pass on the first try. This culture of continuous improvement can dramatically increase efficiency over time.
6. Keep Equipment and Tools in Top Shape
Equipment breakdowns and missing tools are sneaky productivity killers. Implement a system to manage your physical resources:
- Regular Maintenance: Keep to a maintenance schedule for heavy machinery, company vehicles, and power tools. As the adage suggests, prevention is more effective than cure. It’s more efficient and cost-effective to service equipment than to have a critical machine break down in the middle of a job. Downtime from equipment failure can halt a project. Ensuring your forklift or excavator gets its tune-up can be as simple as preventing days of lost time. “Double down on equipment maintenance,” advises one tip; it’s cheaper and more efficient than letting gear fall into disrepair.
- Tool Tracking: Use a checkout system or inventory for tools and small equipment. Workers shouldn’t spend 30 minutes looking for a laser level or waiting for the only functioning nail gun. Having the right quantity of tools and a way to track them (even if it’s just labeling and a sign-out sheet) ensures everyone has what they need when they need it.
- Modern Equipment: If budget allows, invest in newer equipment or technology that can perform faster or with less labor. For example, a telehandler might speed up material staging compared to manual lifting, or a drone could do a quick site survey that saves hours of measuring. Evaluate the ROI of equipment that could streamline tasks.
- Jobsite Organization: An organized jobsite is efficient. Dedicate time to housekeeping; a clean, well-ordered site means tradespeople can find materials and move around without obstruction. Create designated zones for material storage, waste, tool cribs, etc., so that crews aren’t wandering around searching for things.
7. Prioritize Safety and Compliance
At first glance, safety and "efficiency" may not seem directly related, but in reality, they have a deep connection. Safe sites run more efficiently because accidents cause immense disruption.
- Fewer Incidents = Fewer Delays: A single injury can shut down a site for hours or days for investigations and recovery. It also can demoralize the team. By rigorously enforcing safety protocols (PPE use, proper scaffolding, trench shoring, etc.), you prevent accidents that would halt work. Beyond being the right thing to do morally, enforcing safety protocols is financially wise because nearly 1 in 5 workplace deaths occur in construction, and accidents can cost tens of thousands in workers’ compensation and lost time.
- Training in Safety Practices: Regular safety training ensures everyone knows how to do their job without incidents. This includes proper lifting techniques, equipment operation training, and emergency procedures. When crews feel safe and confident, they can work at a positive pace. Work slows down if they are uncertain or concerned about risk.
- Quality Control: Often, the safest way to do something (using the right equipment, not taking shortcuts) is also the way that prevents rework or structural issues. Therefore, safety and quality work together to enhance overall efficiency. For example, properly bracing a structure might take extra time now but prevents a collapse or mistake that would take far more time to fix.
- Compliance Avoids Red Tape Delays: Staying compliant with codes and regulations (safety or building codes) means you won’t suffer work stoppages or fines. Forced shutdowns may result from non-compliance until you address the issues. Proactively meeting standards keeps your project on track.
8. Anticipate and Mitigate Supply Chain Issues
Recently, supply chain disruptions have become a big headache. Delayed materials can idle a project. Improving efficiency today means being proactive about procurement:
- Stay Informed: Monitor market trends for essential materials such as lumber, steel, and appliances. If you know certain items have long lead times or are facing shortages, plan accordingly, order earlier, or find alternate suppliers. Stock up ahead of time, for example, if insulation is scarce during the winter.
- Build a Buffer: Where possible, have a buffer stock of critical materials that have uncertain supply. Some contractors maintain a small inventory of essentials (like common lumber dimensions, fasteners, and wiring) to avoid short-term shortages.
- Flexible Substitution Plans: Identify acceptable alternative products or brands for key items in case your first choice is unavailable. Discuss substitutions with clients ahead of time for critical components. Flexibility can save you from dead stops while waiting for a specific product.
- Strong Supplier Relationships: Nurture relationships with reliable suppliers. They might give you a heads-up on issues or prioritize your orders if you’re a valued customer. Also consider diversifying suppliers so you’re not reliant on a single source for something crucial.
- Contingency in Schedule: A truly efficient schedule accounts for the unexpected. Build some slack into your timeline for potential delays, or overlap procurement activities with earlier phases than usual to account for extra shipping time. As one source noted, after recent disruptions, the best way to overcome supply issues is to “plan ahead and have contingencies if something goes wrong.”
By implementing these strategies holistically, you attack inefficiency from all angles: planning, communication, technology, workforce management, and supply management. The result is a leaner operation where time and money are saved at every stage of a project.
How Bolster Helps You Work Smarter
We’ve discussed many solutions, and you might be thinking, that’s a lot to manage! Using an integrated platform like Bolster can tie everything together and simplify the maintenance of these efficiency practices. By centralizing your operations, Bolster's construction management software enhances efficiency.
- All-in-One Project Management: Bolster combines estimating, scheduling, budgeting, communication, and document storage in one place. No more jumping between apps or spreadsheets; your whole team accesses the same system. This real-time collaboration keeps everyone, including office staff, field crew, and clients, in sync, thereby minimizing miscommunication. For instance, when a schedule change occurs, it automatically updates and sends notifications, thereby removing any confusion regarding version control.
- Financial Tracking and Reporting: With Bolster, you can monitor project financials closely. It provides tools for budgeting, expense tracking, and generating reports. This software helps prevent cost overruns by giving you visibility into spending at all times. When you spot a potential over-budget item, you can adjust immediately (perhaps reallocate resources or negotiate costs) rather than discovering it at the end. Strong financial control is a backbone of efficiency; you won’t be slowed down by cash flow surprises or funding gaps.
- Automation and Workflow Integration: Bolster automates many routine tasks. It can generate invoices, send payment reminders, or create to-do tasks when certain triggers are hit. It also integrates with other tools like QuickBooks for accounting or Excel for data export. Such integration reduces manual data entry and the risk of human error. Your team can focus on actual project work instead of paperwork.
- Centralized Communication: The platform includes messaging and commenting features tied to projects and tasks. Instead of siloed text messages or emails, discussions about a task stay attached. This organized communication allows anyone to review the context at a later time, enabling new team members to quickly catch up. It eliminates lengthy email chains and phone tag, as everyone can see updates in one centralized feed.
- Client Portal: Bolster improves client communication by offering a portal where clients can see progress photos, approve selections or change orders, and send messages. Keeping clients informed makes them easier to work with, speeds up decision-making, and reduces delays. It also cuts down on your team having to respond to constant individual update requests.
- Task Management and Accountability: You can assign tasks (like punch list items or prep work) to specific team members with deadlines. Bolster will track these tasks, send reminders, and allow you to see what’s completed or pending. Everyone is aware of their responsibilities and deadlines, promoting efficiency through accountability.
- Scalability: As your business grows, Bolster grows with you. It helps standardize processes across multiple projects. When you have many jobs running, staying efficient is even more challenging but with a central hub like Bolster, you maintain control and clarity across all of them.
Having such software is “a must-have” to improve and maintain efficiency. Bolster offers comparable advantages, tailored to contractors who want to modernize their operations.
By utilizing Bolster’s features, you effectively implement many of the efficiency strategies discussed, but in a seamless, less labor-intensive way. It’s like giving your contracting business an efficiency toolkit that never clocks out.
Build Faster, Smarter, Better
Improving efficiency in construction is not a one-time task; it’s an ongoing mindset. By identifying bottlenecks, applying smart practices, and leveraging technology, you can achieve significant gains in productivity. Projects will finish faster, crews will be less stressed, clients will be happier, and your profit margins will thank you.
In summary, combat time-wasters by planning thoroughly, communicating clearly, and equipping yourself with the right tools (both in terms of machinery and software). Continuously refine your approach with lessons learned from each job. Even small improvements—saving an hour here, a dollar there—contribute to major benefits over the span of a project (or dozens of projects per year).
Remember that contractor time management isn’t just about the contractor individually being organized; it’s about instilling efficient time use across your whole operation. From management to the field crew to your suppliers, strive to create a culture where everyone values efficiency and knows the plan.
Finally, don’t be afraid to embrace change. The construction industry is evolving with new tech and methods that make work easier and faster. Those who adapt will thrive, while those sticking to “the old ways” may find themselves left behind by more agile competitors.
If you’re ready to take your construction business to the next level of efficiency, consider putting some of these tips into action on your very next project. Even better, consider tools like Bolster to assist you in this journey.
We understand that time is valuable, so we invite you to start saving both time and money today. Visit Bolster to learn more about how our construction management software can help you streamline projects, eliminate inefficiencies, and boost profitability. Don’t let outdated processes slow you down. Embrace the opportunity to build more quickly and intelligently, from the initial plan to the completion of the last nail.